Prof. Dr. – Ing. Vera Hummel
Mechanical Engineer and Doctor of Engineering
Vice-Dean Research and Professor of Industrial Engineering, Smart Factory and Logistics; Head of Werk150, ESB Business School, Reutlingen University
Leads the development of the System Supply Chain Management concept of lectures and seminars supported by La Fondation Dassault Systèmes
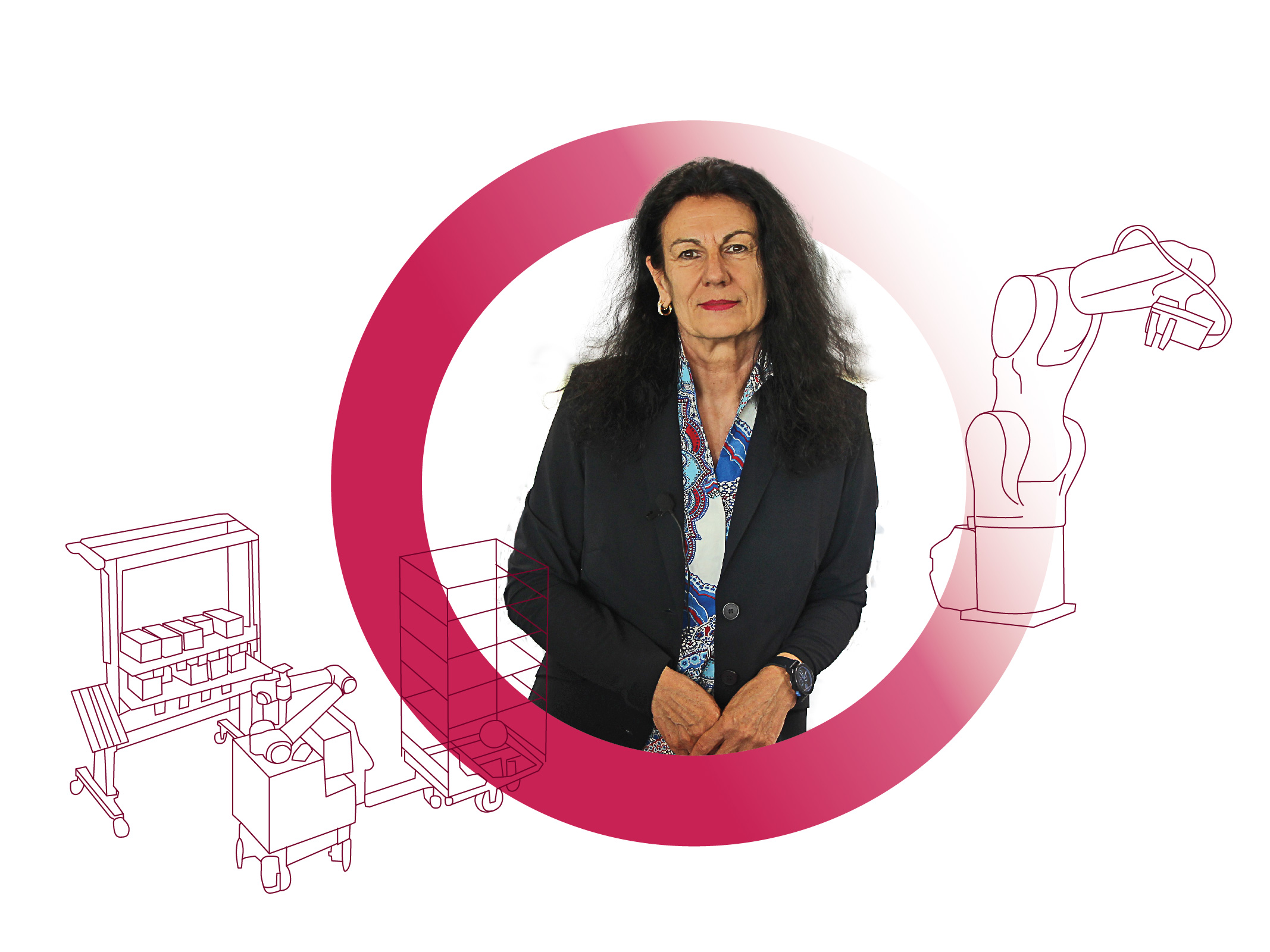
Focus On
The ESB Business School received a grant from La Fondation Dassault Systèmes in 2018 to develop a System Supply Chain Management method to teach skills in supply chain management in a holistic and innovative way. The system approach includes the design, visualization, virtual setup and management of integrated logistics chains with material and information flows across the entire value-added process. It gives students the opportunity to learn skills by simulating logistics scenarios in virtual reality and then experiencing them in the environment of the real learning factory.
From after-school job on an assembly line to mechanical engineering
When she was fourteen years old, Vera Hummel was already sitting on an assembly line during her free time, earning money for her hobbies, to go on holiday and buy nice clothes. It comes as no surprise that some thirty years later she would be setting up one of the first learning factories in Germany.
Growing up, Vera loved technology, mathematics, and physics. It was clear to her that she would be going to a technical high school. There was one in her hometown but at the time, girls were not allowed to join. That is, until Vera was one of the first two girls ever to be admitted. Vera went on to study mechanical engineering at the University for Applied Science in Constance with the support of her parents. “My father, who was a mechanical construction technician, told me that I could study whatever I wanted, whenever I wanted,” Vera explains.
A career bridging industry, research and education
She spent the first six years of her career working for Mercedes Benz in Switzerland and South Africa. She then left the automotive industry to join the renowned Fraunhofer Society working at the Fraunhofer Institute for Production Technology and Automation in Stuttgart in the areas of business excellence, reorganization and quality management. After getting her doctorate, her passion for science and research made her stay as an instructor instead of going back to the industry unlike many of her fellow PhDs at the time.
Spanning industry, research, consulting and education, her varied professional experience led her to believe that research and education should go hand-in-hand. In her current position as Vice Dean of Research at ESB Business School, Reutlingen University, she tries to bring them close together. Students are the experts of the future and it is essential to integrate them in research very early on so they can develop the right new skills. Hands-on training also helps lower the barriers to new technology. It is with this mindset that Vera Hummel developed and implemented a new learning factory after she joined ESB Business School in 2010, the factory Werk150 that she still manages today.
In 2018, she focused her research on “system supply chain management” and received a grant from La Fondation Dassault Systèmes to investigate how integrated business platforms can be used to manage complex systems such as supply chains and develop new methodologies for greater sustainability.
Making a difference
“It is quite interesting to bring in all that new knowledge, the virtual world, virtual twin technology, and the incredible potential of business platforms to a group of young people,” Vera says using the concrete example of a project she is currently running with Master students. Two days a week during fifteen weeks, seven of them develop a new intelligent and personalized product that must also contribute to a circular economy. They go through the whole product life cycle, from generating the idea and defining the model to running simulations and ultimately building the prototype. “One of the most important things in this project is really to enhance the skills of these young people, taking advantage of new technology to enable a different approach for the product development process that takes sustainability into account upfront, thinking about materials, long time usage and recyclability”.
Another advantage of the learning factory is that it provides a safe environment. Contrarily to the real world, if anything goes wrong, it will not stop a production line. Students can simply have another try. “It’s important that everyone has the same access. We can contribute to empowering girls and young women to access science and research by letting them into our factory and motivating them. They are as good as young men are, but due to their background or their social environment, sometimes, they might simply not know it. When we see that they are a little bit hesitant towards new technology, we have to help them overcome their doubts, that’s all.”
In her teaching experience, young men are often more mature going to new technology. When addressing the topic of smart factories and collaborative robots for example, she observes that when they go to the factory floor for hands-on training with the cobots following the theoretical lecture, young women always take a step back while young men will stay in front. It might take them a little longer to go towards new technology but she has also noticed that, once they overcome this barrier and feel more comfortable, young women are more open-minded. They are actually the ones who will stay to practice long after the session is over, until they close the factory at 8 or 9pm. Interestingly enough, in a digital environment, it seems to be the other way around and you can usually see young women using new technology faster than young men.
Inspire and empower
Drawing on her personal experience, Vera Hummel would like to share a few messages with girls and young women. “Follow your truth and your path. Do not give up, whatever you want to do, do it. And whenever you start something, finish it, never stop halfway through”. She also stresses the importance of mentorship programs. “Don't be shy. If you can find a mentor, seize this great opportunity to have a partner with whom you can discuss openly about the evolution of your career, skills you are missing, things you still need to learn. This is so valuable”.
She knows the significance of having a person you can count on. There was a time in her career, when she had to choose to either leave the company she was working for – in 1986, as a young woman engineer in a traditional company, it was not always easy – or asking for support and pulling through. She chose the latter, reaching out to the then CEO of Mercedes Benz in Switzerland who had offered his help the first time they met and who stood by her side throughout her early career. Later on, she could also rely on her department head at Fraunhofer IPA for encouragement.
In a similar way, she also advises to start networking as early as possible, stressing the need to build contacts and maintain them via school networks, student networks, and professional associations.
She concludes with one last piece of advice: “Whenever in a leading position, always remember that you are only as good as your team is. That learning factory behind me would never work in the digital area without Beate Brenner, my fellow researcher. I need the whole team to develop it further. You cannot do it on your own, and if you do not appreciate that, it will simply not work in the long run”.